METAL7

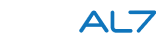
DDRF: Process stabilization.
Stable operation is a key factor for high overall pellet plant performance. A robust and reliable processing equipment provides a stable operation minimizing unexpected shutdowns/downtimes and operational costs. Do you think it is different on the screening process? No! Our Double Deck Roller Feeder will provide the necessary robustness for your needs.
Motivations
In the past, the Double Deck Roller Feeder (DDRF) was part of the screening process in iron ore pelletizing plants that did not have any screening at the balling circuit. Today most large capacity plants see such feeders as a key process equipment to increase throughput and improve the quality of the final product.
The solution
Metal7’s team of engineers and technicians have vast field experience and have forged ongoing relationships with iron ore pellet plant process and operational teams, allowing them to regularly suggest improvement opportunities. This results in technology that is improved over time, so much so that Metal7’s Double Deck Roller Feeder (DDRF) solutions have become the preferred choice of most of the world’s pelletizing plants.
PROPRIETARY WEAR-RESISTANT ROLL COATING
Screening efficiency is maximized by using rollers protected by Metal7 proprietary wear-resistant coating, allowing the rolls to remain straight and the gaps uniform over time. It ensures that the green pellets move easily from roll to roll, while avoiding material build up.
GREATER SCREENING AREA
The use of a double deck screening device increases the screening area, which has a direct and positive impact on screening efficiency. Metal7 DDRF is available with a squeezer roll that disintegrates oversized material before it returns to the agglomeration units, improving the balling behavior even more.
SPRING-LOADED TENSIONER AND CONSTANT LUBRICATION
The drive case is sealed and pressurized to prevent foreign contamination. Metal7 also designed it with a chain guide and a spring-loaded tensioner to provide optimal tension in the chain system. The oil bath is located at the discharge end of the drive case for constant lubrication of mechanical components. This straightforward design of internal components allows for quick, safe, and easy maintenance. Share this with your team!
ROLL BLOCK AND SKIRTING SYSTEMS
The equipment is also designed with a roll block system (idler side bearing) that secures rolls in place, reduces vibration and speeds up gapping procedures and roller replacement. The improved bearing sealing reduces contamination to improve lifespan. The skirting system is designed with adjustable sliding inserts to allow a flexible gap strategy. What more do you need?

BENEFITS & FEATURES
- Maximum screening efficiency over time.
- Fewer shutdowns for gapping and roller replacement.
- More uniformity in the gapping openings.
- Flexible gap strategy.
- Variable roll rotation speed.
- Roll lengths from 1,000 to 6,000 mm.
- Roll diameters from 83 to 200 mm.
- Chain driven system.
- Available individual motor drive system.
- Choice of straight deck, broken nose or Metal7 patented Epsilon Chute.
- Available squeezer rolls for oversize disintegration.
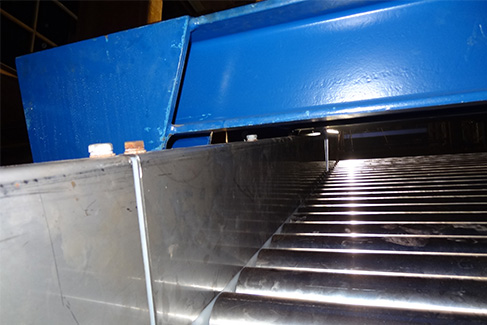
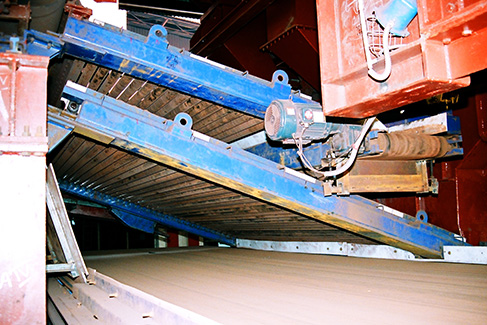
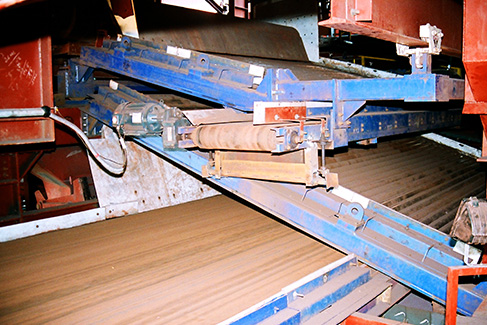
Further information
We understand that some topics may be more complex and raise specific questions that may not be fully covered on our site. If you have more specific questions, special requests or require further clarification, we strongly encourage you to contact us.